Projects/ Metallurgy
Electrical Furnace Reconstruction for Fusing Copper-Bearing Materials in the Electrothermal Unit of Electrolysis Workshop of JSC Kazzinc
Customer JSC Kazzinc, Ust-Kamenogorsk
The technological process description:
The electro-furnace is a pyrometallurgical set of a closed type which operates under discharge having caisson slag belt and is cooled by furnace hearth. The furnace is round and has three electrodes, canned with metallic covering. In the furnace crown there is a charge hole besides the electrode holes. In the places of electrode input some caissons are set and serve as restraint devices. Water inlets to cool the caissons give the possibility to control water volume and temperature.
Just next to the furnace there is an emergency pit with volume capacity to take the entire fused electrolyte in the furnace in case of emergency and accidental breakout through the furnace lining.
The slag temperature 1250-1300 ? and it is achieved on a count of Joulean heat which is evolved in the inter-electrode gap of furnace slag bath. Loaded by the collection crew into the slag bath the furnace-charge is fused and further executed by sulfdizing fusing the result of which is black lead, matte, speiss, slag and gases. The electrolytes of black lead, matte, speiss and slag are divided in the furnace layer by layer on a count of different leak tightness.
The lead tapping is produced into casting forms of recasting type which are set on a moving driveless truck with an electric drive. Over the casting forms there is an enclosure to provide outgassing.
The matte tapping is produced into casting forms of recasting type which are set on a frame in the closed box with exhaust ventilation.
The slag tapping is produced into casting forms of non-recasting type and set on driveless truck with an electric drive. While the casting forms filling with slag the capsule is moving. Over the casting forms there is an enclosure to provide outgassing.
The gas evolved in the process of sulfdizing fusing is emitted through a short main flue into the system of gas cooling and clearing. The system consists of afterburner and inertia-type deduster, coolers and centrifugal collector. After coming through the centrifugal collector the gas is primary refined by flue-gas fan -15 and goes to fine gas cleaning in the units of dust collecting at the lead production workshop.
The purpose and characteristics of automated control system:
The automated control system for the present project is elaborated for operating slurry electrofusing furnace in the electrothermal unit of Ust-Kamenogorsk Metallurgical Complex Kazzinc.
The system is for automated process of slurry fusing in the furnace getting all the necessary information concerning the whole process.
Automation system descriptions and characteristics:
The automated control system is of three levels.
the upper level is an engineering workstation of an operator;
the middle level is a programmed controller Delta-V Emerson;
the lower level are sensors and actuating devices of the technological equipment.
The upper level is based on to central control computers.
The functioning of the leading elements is carried out by the controllers in the middle level Delta-V which also realize signals input-output at the local devices and do all the necessary calculations, control the actuating devices and transfer the data to the computers of the upper level.
The lower level of the automated control system is represented by the technological equipment sensors of Manotherm, Endress-Hauser, Bero.
The system produces the following functions:
data collecting from the sensors set on the technological equipment;
the received data processing and giving all the necessary control signals;
technological parameters indication and control loop parameters and the equipment operation status in the form of graphic symbolic circuits at the display of the operators engineering workshop;
signaling parameters stepping out technological and emergency limits by background color change of the measuring parameter;
the possibility to choose manual or automatic mode control of the technological process from the operators board providing supervising controlling in manual mode and digital controlling in automatic mode;
the possibility to control a separate regulator in manual or automatic mode;
technological information accomplishment, paperwork management and storage of measured technological parameters, notification of technological process failures with keeping non-compelled alarm and current signals and system operation protocol;
technological data and protocols printing on requirement of an operator;
multilevel access into the automated control system via individual password system on the following categories: an operator has an access to a new shift registration, a control measuring devices engineer can correct the parameters chart, a technologist can correct the parameters limits, a craftsman can operate the devices, correct the parameters limits, the passwords list and logging off, a system administrator has an access to all the functions;
keeping the access diary to the automated control system fixing the time of technological parameters changes, their new and old values;
the possibility to administrate the system and the look through its status by means of remote access;
context prompts getting concerning all the basic functions.
The system is open for expanding information and functional capacities when reserving input-output of controllers hardware in 15 per cent of the project size.
Automated and control functions description:
The system of automatic control the technological parameters includes:
four furnace- charge dozers control;
flow transport system: by two transporters, collection crew and an elevator;
The furnace three electrodes positions control
Four flue-gas fans control and the control of their louvers and valves;
Discharge upkeep in the furnace and flues by means of flue-gas fans;
Constant load and upkeep on the electrodes by means of their remote control moving in the operators workshop;
Constant percentage of furnace-charge composition by means of four dozers control.
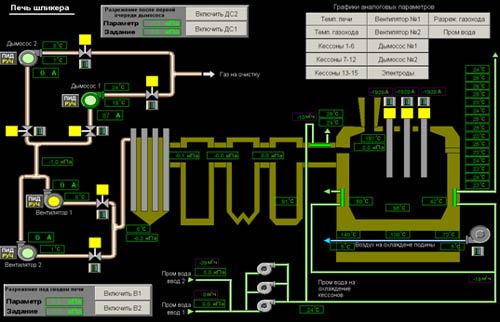
The symbolic circuit Slurry furnace
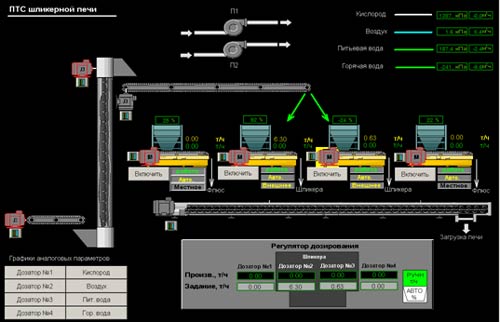
The symbolic circuit Slurry furnace
The system was put onto operation in 2009.
|